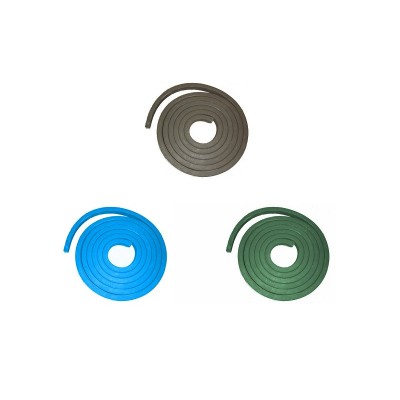


Plastic hoses
Spiral hoses for water and foodstuff Heavy spiral hoses for various uses (drainage, waste water, pumping, etc.) Spiral hoses for ventilation and suction Braided hoses Monoextruded hoses, flexible hoses and spirals Spiral hoses for drains, waste water, abrasives, oils and acids Composite hoses
Spiral hoses for water and foodstuff Heavy spiral hoses for various uses (drainage, waste water, pumping, etc.) Spiral hoses for ventilation and suction Braided hoses Monoextruded hoses, flexible hoses and spirals Spiral hoses for drains, waste water, abrasives, oils and acids Composite hoses

Fittings and clamping systems
Compressed air couplings Fittings for concrete Vic and Vical fittings Storz Couplings Sandblast couplings Agricultural Couplings Camlock Couplings Hydraulic fittings Pneumatic fittings Pump and TOF fittings Fuel fittings Stainless steel fittings Valves, gate valves, taps and various fittings Spalock clamps Hose clamps Tape clamps Joint sleeves for ventilation pipes Manometers, thermometers and various indicators
Compressed air couplings Fittings for concrete Vic and Vical fittings Storz Couplings Sandblast couplings Agricultural Couplings Camlock Couplings Hydraulic fittings Pneumatic fittings Pump and TOF fittings Fuel fittings Stainless steel fittings Valves, gate valves, taps and various fittings Spalock clamps Hose clamps Tape clamps Joint sleeves for ventilation pipes Manometers, thermometers and various indicators

Systems Engineering: Hoses and fittings
AFL cast iron fittings Aliaxis fittings - FIP GE Aliaxis fittings - Astore Fittings and Couplings - other manufacturers Metal flanges PVC pipes PVC-C pipes PVDF pipes PP pipes PE pipes Tubi rigidi in PMMA PC pipes Fire prevention - Vic fittings Fire prevention - Components Pipes in ferrous and non-ferrous materials Electrically heated tubes
AFL cast iron fittings Aliaxis fittings - FIP GE Aliaxis fittings - Astore Fittings and Couplings - other manufacturers Metal flanges PVC pipes PVC-C pipes PVDF pipes PP pipes PE pipes Tubi rigidi in PMMA PC pipes Fire prevention - Vic fittings Fire prevention - Components Pipes in ferrous and non-ferrous materials Electrically heated tubes

Rubber, plastic and materials for gaskets
SBR rubber sheets NBR nitrile rubber sheets EPDM rubber sheets CR chloroprene rubber sheets NR para and anti-abrasive rubber sheets Special rubber sheets Granulated rubber sheets Rubber mats and anti-fatigue mats Technical floors PMMA methacrylate PC polycarbonate PETG Rigid PVC PA polyamides PTFE PP polypropylene Flexible PVC PE polyethylene PU polyurethane and Poliucell Bakelite and fibroid Felt and filtration Oilproof paper for gaskets Laminated glass Mousse foams PE foams Silicone foams PVC foams Sponge foams Polyurethane foams Isolgom foams Non-sintered PTFE foams Special plastics (PEEK, PVDF, Torlon…) Asbestos-free seals - Heat-insulating refractories Asbestos-free seals - Yarns, packing and various Asbestos-free seals - Joints and graphite sheets Custom products O-Rings and scrapers Technical fabrics Rubber drawn parts Conveyor belts, transmission belts and similar products Pressed cardboard for gaskets
SBR rubber sheets NBR nitrile rubber sheets EPDM rubber sheets CR chloroprene rubber sheets NR para and anti-abrasive rubber sheets Special rubber sheets Granulated rubber sheets Rubber mats and anti-fatigue mats Technical floors PMMA methacrylate PC polycarbonate PETG Rigid PVC PA polyamides PTFE PP polypropylene Flexible PVC PE polyethylene PU polyurethane and Poliucell Bakelite and fibroid Felt and filtration Oilproof paper for gaskets Laminated glass Mousse foams PE foams Silicone foams PVC foams Sponge foams Polyurethane foams Isolgom foams Non-sintered PTFE foams Special plastics (PEEK, PVDF, Torlon…) Asbestos-free seals - Heat-insulating refractories Asbestos-free seals - Yarns, packing and various Asbestos-free seals - Joints and graphite sheets Custom products O-Rings and scrapers Technical fabrics Rubber drawn parts Conveyor belts, transmission belts and similar products Pressed cardboard for gaskets

Hardware, tools and equipment
Foils, covers and bags Adhesives, sealants and chemicals Adhesive tapes Packaging items Bellows Anti-vibration Small parts Wheels Lifting, tie rods and anchoring Welding Hand tools, instruments, boxes and accessories Electric and pneumatic tools, machinery, pumps and accessories Furnishings and housewares Items from wire rod Fixing Electrical equipment Wiring Cutting and deburring discs Chuck bits and accessories Anti-vibration and molded rubber articles
Foils, covers and bags Adhesives, sealants and chemicals Adhesive tapes Packaging items Bellows Anti-vibration Small parts Wheels Lifting, tie rods and anchoring Welding Hand tools, instruments, boxes and accessories Electric and pneumatic tools, machinery, pumps and accessories Furnishings and housewares Items from wire rod Fixing Electrical equipment Wiring Cutting and deburring discs Chuck bits and accessories Anti-vibration and molded rubber articles

Special articles for construction
Waterstop and hydro-expansive lists Fenders Rubber bearing pads and supports Ventilation duct Steel pipes with Vic ends Tunnel Hose Packers and shutters Lances and nozzles for spritz beton Stators and rotors for plastering machines Centering device for erector and H profiles for TBM PU scrapers Special rubber profiles and rubber joint covers Protection net for underground pipes Concrete and plastic spacers Plaster panels Hoppers and containers with opening bottom Para sleeves and plastic conveyor tubes Metal and plastic trunks Heating bands for drums Waterproofing items Inflatable neoprene hose Diaphragm gasket Resins and chemicals Stators and rotors for plastering machines
Waterstop and hydro-expansive lists Fenders Rubber bearing pads and supports Ventilation duct Steel pipes with Vic ends Tunnel Hose Packers and shutters Lances and nozzles for spritz beton Stators and rotors for plastering machines Centering device for erector and H profiles for TBM PU scrapers Special rubber profiles and rubber joint covers Protection net for underground pipes Concrete and plastic spacers Plaster panels Hoppers and containers with opening bottom Para sleeves and plastic conveyor tubes Metal and plastic trunks Heating bands for drums Waterproofing items Inflatable neoprene hose Diaphragm gasket Resins and chemicals Stators and rotors for plastering machines

Safety - Personal Protective equipment
Star BZ workwear Star Winter workwear Star workwear Basic workwear Winter workwear Promotional workwear Special workwear Disposable clothing, gloves and masks Raincoats and rain boots Heat-resistant workwear and gloves Leather gloves NBR gloves Synthetic coated gloves Mapa gloves Cut-resistant gloves and accessories Neoarm safety shoes Cofra safety shoes U-Power safety shoes Beta safety shoes Base safety shoes Gasport safety shoes Diadora safety shoes Puma safety shoes Dunlop safety shoes Sir shoes Industrial Starter shoes Portwest shoes Decathlon shoes KA shoes Rays shoes Lotto shoes Exena shoes Dike shoes Coverguard shoes Safe Way shoes Boots Safety boots Work socks, insoles and accessories Breathing - Half masks Breathing - Full face masks Vision protection Hearing protection Head protection
Star BZ workwear Star Winter workwear Star workwear Basic workwear Winter workwear Promotional workwear Special workwear Disposable clothing, gloves and masks Raincoats and rain boots Heat-resistant workwear and gloves Leather gloves NBR gloves Synthetic coated gloves Mapa gloves Cut-resistant gloves and accessories Neoarm safety shoes Cofra safety shoes U-Power safety shoes Beta safety shoes Base safety shoes Gasport safety shoes Diadora safety shoes Puma safety shoes Dunlop safety shoes Sir shoes Industrial Starter shoes Portwest shoes Decathlon shoes KA shoes Rays shoes Lotto shoes Exena shoes Dike shoes Coverguard shoes Safe Way shoes Boots Safety boots Work socks, insoles and accessories Breathing - Half masks Breathing - Full face masks Vision protection Hearing protection Head protection